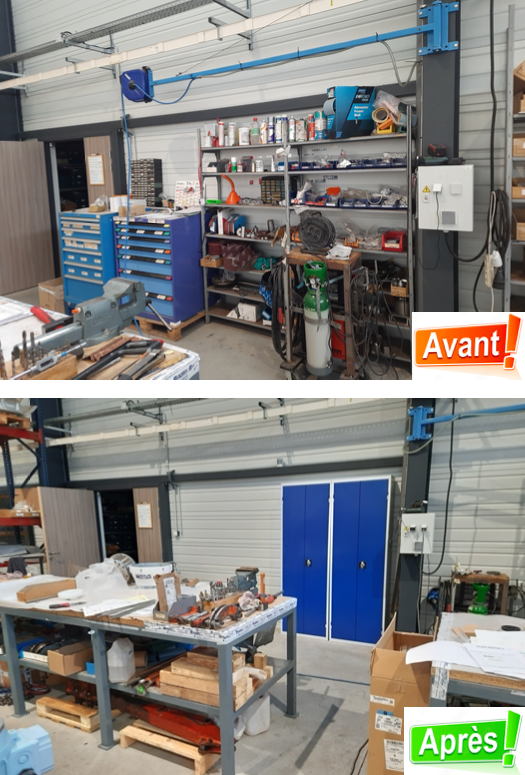
Actualités
MAXIMISER L'EFFICACITÉ ORGANISATIONNELLE : la mise en place de la méthode 5S
Dans un paysage professionnel où la concurrence est accrue et les demandes des clients toujours croissantes, chaque avantage en matière d'efficacité et de productivité compte. L'une des approches les plus efficaces qu'a trouvé AGITEC pour atteindre ces objectifs est la méthode 5S. Cette pratique de gestion visuelle et d'organisation qui trouve ses origines dans les principes du lean manufacturing (méthode d'optimisation qui vise à réduire le temps nécessaire à la production).
Popularisée par Toyota dans les années 1950, la méthode 5S est aujourd'hui largement adoptée dans divers secteurs industriels. Son impact dépasse largement la simple organisation des espaces de travail ; elle englobe une culture d'amélioration continue et d'ordre, éléments essentiels pour la réussite à long terme de toute organisation.
Qu'est-ce que l'organisation 5s ?
La méthode 5S est bien plus qu'un simple système d'organisation de l'espace de travail ; c'est une philosophie de gestion visuelle qui vise à créer un environnement de travail optimal, propice à la productivité, à la sécurité et à la qualité. Les cinq "S" proviennent des termes japonais Seiri (Trier), Seiton (Ranger), Seiso (Nettoyer), Seiketsy (Standardiser) et Shitsuke (Suivre). Chacun de ces principes représente une étape clé dans le processus d'organisation et de maintien de l'efficacité dans un environnement professionnel. En combinant la discipline organisationnelle avec une approche centrée sur les personnes, la méthode 5S favorise une culture de responsabilité partagée et d'amélioration continue au sein des différents espaces de travail de l'entreprise.
LA MISE EN PLACE DE L'ORGANISATION 5S CHEZ AGITEC
Interview de Samoa MILARET, Responsable QSE
"Au cours des derniers mois, l'augmentation significative de la production avait provoqué un surplus de matériel dans l'atelier de production alors même que d'importants investissements pour doubler la surface avaient eu lieu trois ans auparavant. En parallèle, certains collaborateurs exprimaient le désir de revoir leurs méthodes de travail pour accroître la productivité et l'efficacité. Face à ces défis, nous devions trouver un moyen d'optimiser les espaces de travail tout en renforçant la sécurité au sein de notre atelier de production d'agitateurs industriels sur-mesure. C'est ainsi que nous avons décidé de mettre en oeuvre la méthode des 5S, une approche déjà approuvée par d'autres industriels.
Pour faciliter cette transition organisationnelle, AGITEC a bénéficié du programme Ambition du CETIM, accompagné par la Région Auvergne Rhône-Alpes. Après un diagnostic approfondi de l'entreprise, la définition des objectifs et l'élaboration d'un plan d'action, nous disposons de tous les outils nécessaires pour appliquer la méthode des 5S au sein d'AGITEC.
la mise en place
Après avoir déterminé que la zone "montage" de notre atelier de production serait la première à bénéficier de cette démarche, nous avons constitué un groupe de travail réunissant les acteurs concernés : le chef d'atelier, les techniciens-monteurs et le réceptionniste-magasinier. Cette zone, nécessitant un réaménagement majeur pour accroître son efficacité, revêt également une importance en tant que vitrine de l'entreprise lors des visites clients par exemple.
- La première phase a consisté à trier le matériel et l'outillage commun aux collaborateurs, en ne conservant que l'essentiels. Ensuite, chaque collaborateur a trié son matériel spécifique en lui attribuant un code couleur pour symboliser son appartenance.
- La deuxième phase a impliqué un nettoyage complet de la zone : sol, établis, étagères, tout a été passé au crible.
- La troisième phase a été marquée par l'organisation de l'espace, avec l'attribution d'un emplacement défini pour chaque matériel. Grâce à un code couleur ou un marquage au sol, chaque élément est désormais associé à un espace précis dans la zone de travail.
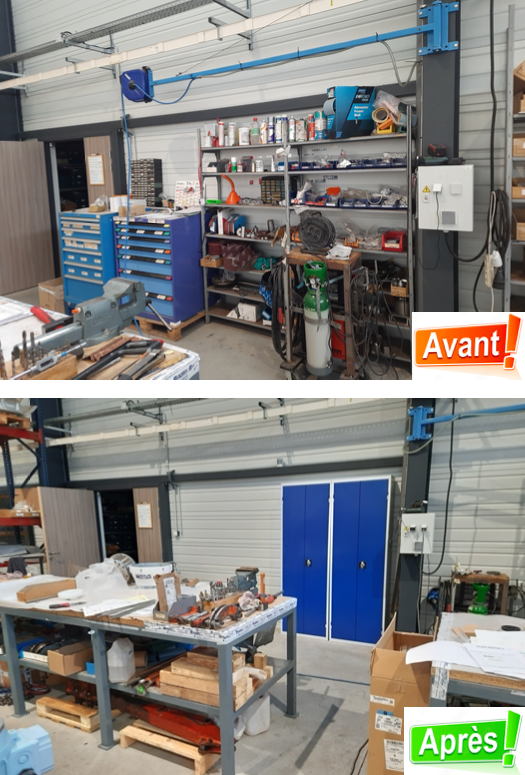
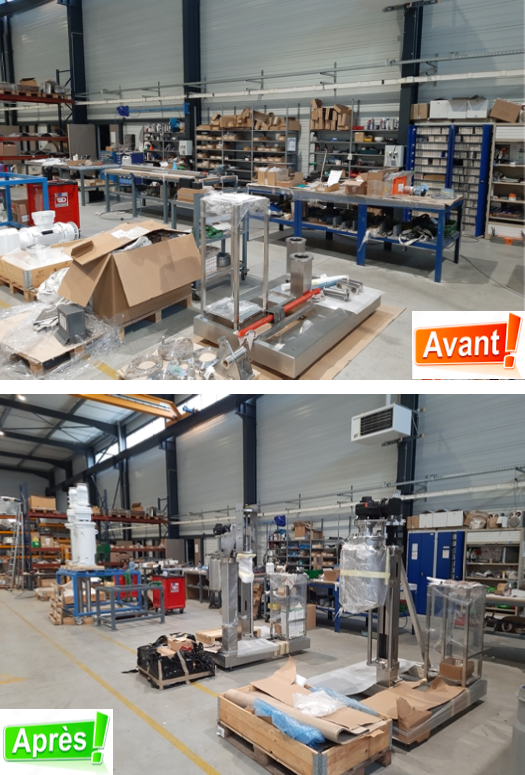
- Enfin, la quatrième et dernière phase a consisté à formaliser l'application de la méthode en établissant des standards de rangement et des règles de nettoyage. Des documents visuels, tels que des plans ou des photos des lieux, ont été placés à différents endroits pour assurer la continuité de la démarche.
L'engagement des collaborateurs
Pour susciter un engagement maximal, les collaborateurs ont assisté à une réunion où la méthode, ses enjeux et ses bénéfices ont été présentés. Cette initiative a rapidement reçu un accueil favorable puisque les collaborateurs étaient eux-mêmes demandeurs d'améliorations en matière d'organisation de leurs espaces de travail.
Les résultats
Les résultats ont été perceptibles dès les premiers jours : la zone "montage" était plus dégagée, mieux rangée, ce qui a rendu l'espace de travail plus agréable au quotidien. Les collaborateurs ont apprécié évoluer dans un environnement propice à l'accomplissement de leurs tâches.
A l'avenir, l'entreprise envisage d'étendre cette méthode à d'autres zones de l'atelier, voire aux bureaux, notamment pour le rangement administratif."
En conclusion, la mise en place de la méthode des 5S a un impact significatif dans l'optimisation des espaces de travail et l'amélioration de l'efficacité opérationnelle au sein de l'entreprise. Grâce à une approche méthodique et collaborative, AGITEC a réussi à transformer la zone de production, en réduisant le désordre, en instaurant des standards de rangement et de nettoyage, et en favorisant un environnement de travail sûr et productif. Avec des résultats tangibles dès les premiers jours, l'entreprise envisage désormais d'étendre la méthode des 5S à d'autres espaces de travail.
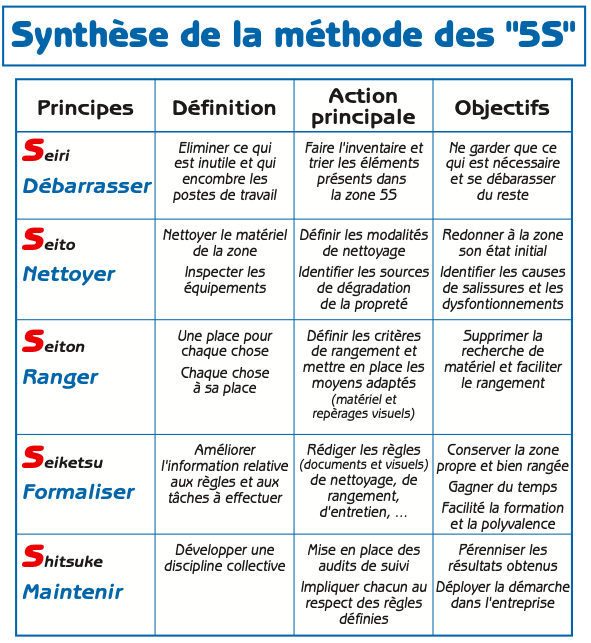